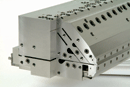
The coating die (ie, close to the coating method) regulates the flow of the coating liquid at a constant speed in advance, and acts as a completely closed system, reducing the air emissions problem, and therefore compared to the traditional roller coating method. More efficient and easier to control. The development of a multi-runner slot die enables processors to paint two or more layers at a time, bringing productivity and quality advantages to a whole new level.
The multi-pass Ultracoat die can also be used in other applications such as applying a silicone release layer and a pressure sensitive adhesive simultaneously while the paper is being painted, and applying the electrolytic and cathode layers to the thin film battery.
The flow channel is the flow channel within the die, which distributes the coating liquid to a predetermined final product width to form a uniform flow profile and reach a predetermined thickness. In a two-pass or three-pass die, each coating's liquid undergoes this process in its own flow path before it forms a multilayer structure with other coating materials.
The EDI engineer designed the die to produce a laminar flow of the coating (the coating is still evident after the coating material is bonded), thus successfully developing a multi-pass Ultracoat system. The viscous liquid is more likely to achieve laminar flow, like the flow of molten resin in a coextruded plastic. For the less viscous liquids used in the coating, EDI designed a streamlined system so that no disruption or material mixing occurs at different levels.
Bedside Table,Bed Side Table,White Bedside Table,White Nightstand
CAMOSA HOME , https://www.camosa-funiture.com